CapU Theatre Technician 3D Prints Face Shield Parts for Healthcare Workers
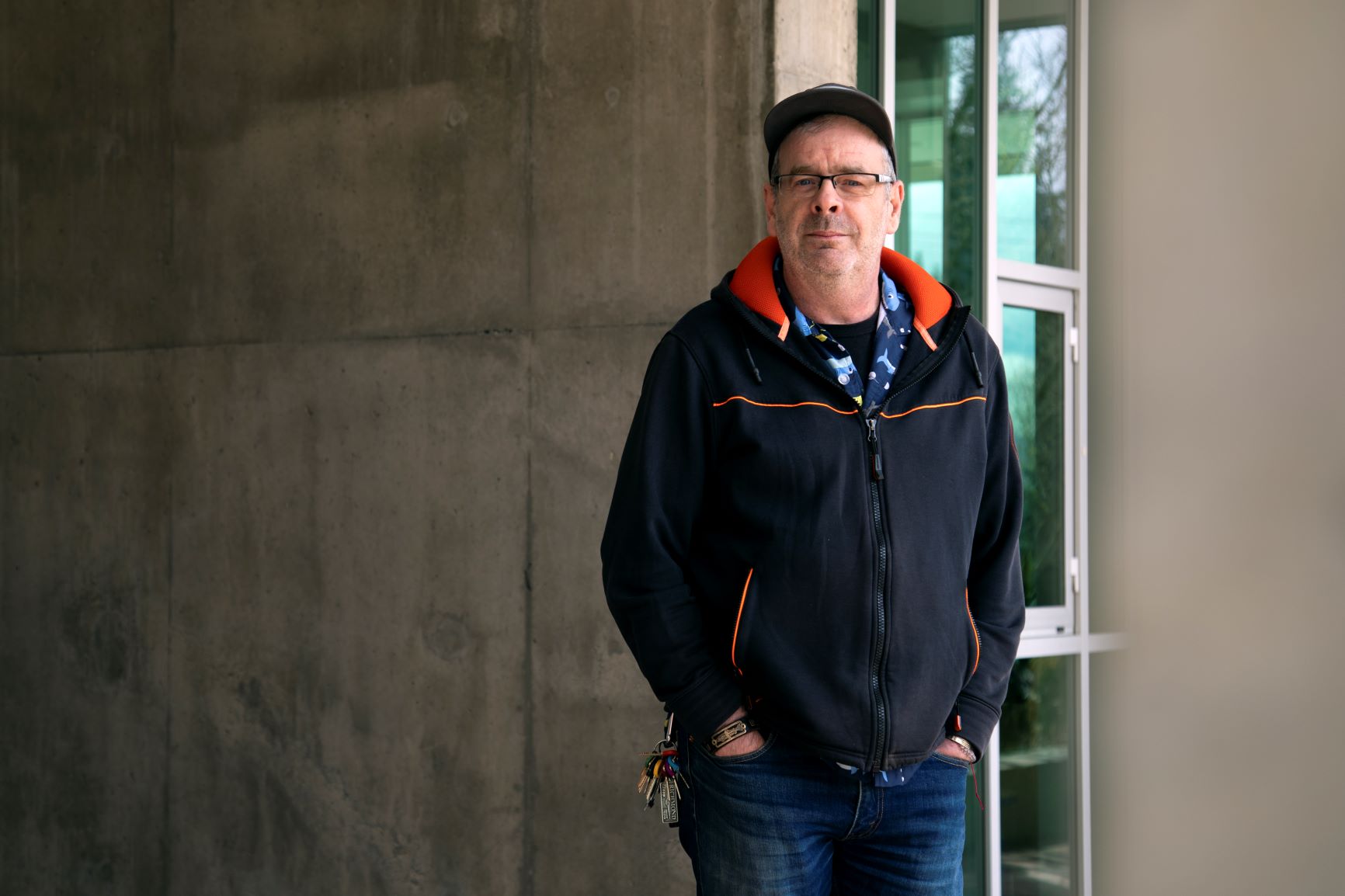
Since the onset of COVID-19, basic items healthcare professionals need to stay safe on the job – masks, hand sanitizer, wipes, rubbing alcohol – have become hot commodities, with people hoarding and occasionally trying to profiteer off stock shortages and a panicking public.
Sparky Lawrence, technical director for the BlueShore Theatre at Capilano University, saw a solution to the shortage of face shields and was able to mix it with his hobby of 3D printing.
“I got into 3D printing on a whim,” he says. “It’s a hobby, but it’s fun to design things for practical use.”
So far, Sparky’s projects include creating a larynx made with a flexible filament, so musical theatre instructors can demonstrate how the organ works for singers, a set of 100 candles to hang above the stage during the winter production of MacBeth and a fishing reel, for his other hobby.
When he heard about the shortage of emergency medical equipment, he connected through a Facebook group with like-minded makers – a term used in the DIY community for artisans who create tangible objects using open-source software – to do his part.
“The open source community is really on top of things,” he says. “If you’re having a problem with something, usually someone in the [maker] world will be able to help you out.”
Using software developed by an entrepreneur in the Czech Republic, Sparky prints headbands for medical face shields. Other makers are using their machines to create the other components, including laser cutting 0.5-milimetre thick sheets of plastic resin create the clear shield.
“Most people only have one machine,” he says. “This is why the manufacturer, LNG Studios, is coordinating everyone.”
Each headband takes more than three hours to print, but with his printer running 24/7, he’s produced more than 30 and will be delivering them to the manufacturer which assembles the shields in-house.
“They take the components from all the other makers and build them,” he says.
Once all the pieces are in one place, shields can be assembled in as little as 10 minutes and can be cleaned and re-used. The first batch of 120 shields was delivered to a hospital last week.
“It’s not just hospitals that need them, first responders, dentists and all kinds of people are looking for them,” he says. “I think we’re going to be busy for a while.”
Submitted by: Communications